Introduction
Diamond Turning (Single Point Diamond Turning) is a manufacturing process used to quickly produce low to moderate volumes of highly accurate plastic optics, usually to support R&D or prototyping efforts.
The machine that does the single point diamond turning is a precision CNC lathe. The cutting tool is a diamond that has been specially prepared to cut the required surface geometry of the lens. Diamond turning is used to create light weight aspheric plastic lenses and is capable of cutting freeform polymer optics as well. Because the surface is generated on a CNC lathe, the process is very deterministic and highly repeatable, with surface form errors as low as 2 waves per 2.5 cm of diameter. Because the cutting tool is actually a diamond, surface finishes of 3 to 4 nanometers (Ra) are regularly achieved. With surface finishes this fine, the diamond turned optics are very specular, require no post-machine polishing, and can be readily coated with either a multi-layer thin film coating, for enhanced transmission.
| 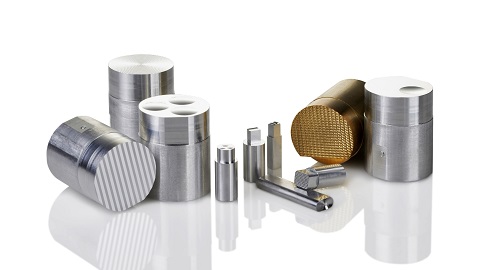
Product Brochure Link: 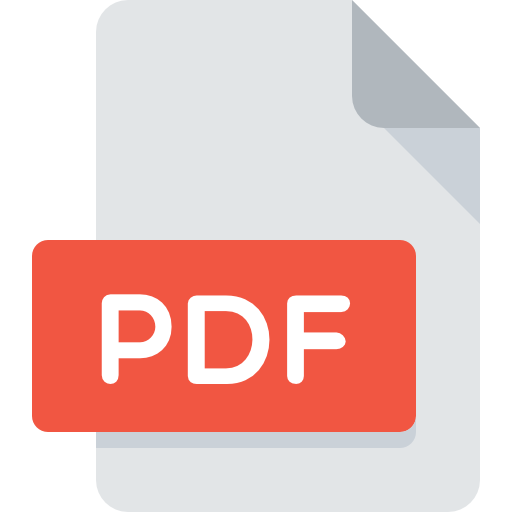
Contact us at info@simtrum.com for customized service |
Customer-Specific Ultra-Precision Tool Inserts ● Elliptical Fresnel ● Micro Lenses ● Racetrack Fresnel ● Aspherical ● Concentric Lines ● Spherical ● Micro Lens Array ● Freeform ● Linear Fresnel ● Pyramid ● Fly Eye Lens ● Toric
| 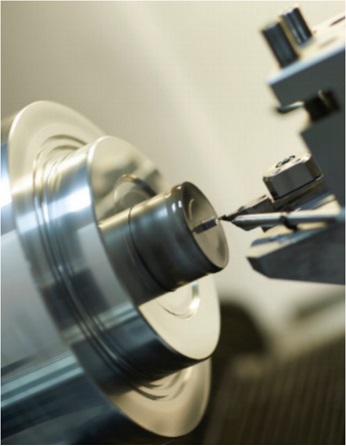
Diamond Turning Tool Inserts |
Established DT Tool Insert Materials ● Aluminium, Brass, Copper, Beryllium Copper ● Nickel-Phosphor ● Steel
| 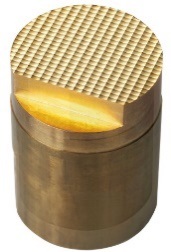
|
Direct Diamond Turning on Plastics ● Zeonex Cyclo Olefin Polymer (COP) ● Polymethyl methacrylate (PMMA) ● Polycarbonates(PC)
| 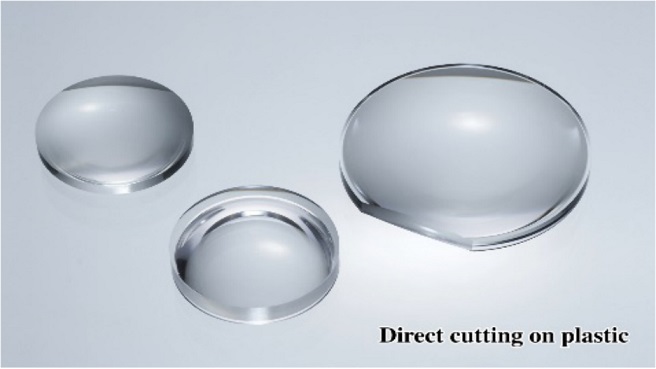
Direct Diamond Turning on Plastics |
Single Point Diamond Turning(SPDT) Lathes ● 3 - Axis (Moore's Nanotech) ● 5 - Axis (Moore's Nanotech) ● Son-X Ultrasonic Attachments
| 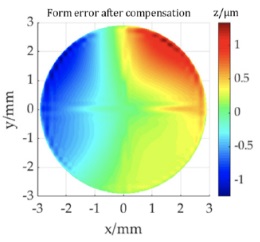
Submicron Forth Accuracy, Ra<5um |
Our Equipments DKSH Nanotech 250UPI V2 Compact diamond turning lathe
● Diamond Turning Lathe with 3 axes to produce spherical & aspheric optical lenses, mirrors, mold pins, freeform optics and mechanical components. ● Sub-nanometer level surface finishes and sub-micron form accuracies, directly off the machine in a wide variety of materials. ● Workpiece capacity of Ø300mm and 200mm long. ● Granite base structure with passive air isolation system ideal for ultra precision needs.
|
Features
- Compact Diamond Turning Lathe - Optional C Rotary with Linear Y or Rotary B Axis - Mechanical design Strengths | 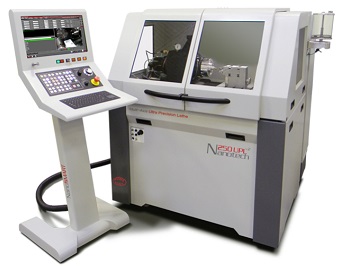 |
Technical Data
|
|
|
General | Description |
System Configuration | Ultra-Precision two, three, or four axis CNC contouring machine with “T” axis orientation |
Workpiece Capacity | 300mm diameter x 200mm long (150mm diameter swing capability over the optional rotary B-Axis) |
Programming Resolution | 0.01 nanometer linear / 0.0000001° rotary |
Functional Performance (As measured with laser interferometer & white light interferometer on same part) | Material – High Purity Aluminum Alloy Form Accuracy (P-V): ≤ 0.1µm / 75mm diameter, 250mm radius convex sphere. Surface Finish (Ra): ≤ 2.0 nanometers (Important Notice: Both Form & Surface Finish measured on the same part, same surface!) |
Working Load Capacity (Radial) | 85 Kg @ 7bar (185 lbs @ 100psi.) / 102 Kg @ 10bar (225 lbs @ 145psi.) @ spindle nose |
Working Load Capacity (Axial) | 197 Kg @ 7bar (435 lbs @ 100psi.) @ spindle nose |
Axial Stiffness | 228 N/μm @ 7bar (1,300,000 lbs/in @ 100psi) / 260 N/μm @ 10bar (1,500,000 lbs/in @ 145psi) |
Radial Stiffness (at nose) | 98 N/μm @ 7bar (560,000 lbs/in @ 100psi) / 140 N/μm @ 10bar (800,000 lbs/in @ 145psi) |
Motion Accuracy | Axial: ≤ 12.5 nanometers (0.5μ”) Radial: ≤ 12.5 nanometers (0.5μ”) |
DKSH Nanotech 650FG V2 Compact diamond turning lathe
● Diamond Turning system with expandable to 5 axes of linear X, Y, Z , and rotary B, C axes. ● Vertical oil hydrostatic Y-axis with symmetrically integrated main work spindle make it more advanced machining techniques such as raster flycutting of linear diffractives and freeforms, micro-prismatic optical structures and micromilling of aspheric lens arrays possible. ● Workpiece capacity up to Ø650mm and 300mm long.
|
Features - Most Versatile Freeform Generator. - Unique Y-axis Design Proven Exceptional - Mechanical Design Strengths | 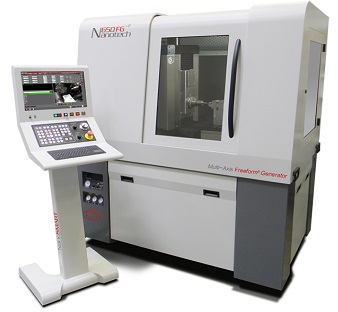
|
Technical Data |
|
General | Description |
System Configuration | Ultra-Precision three, four, or five axis CNC machining system for on-axis turning of aspheric and toroidal surfaces; slow-slide servo machining (rotary ruling) of freeform surfaces; and raster flycutting of freeforms, linear diffractives, and prismatic optical structures |
Workpiece Capacity | 650mm diameter x 300mm long (Note: additional swing capacity available upon request) |
Programming Resolution | 0.01 nanometer linear / 0.0000001º rotary |
Functional Performance (As measured with laser interferometer & white light interferometer on same part) | Material – High purity aluminum alloy. Form Accuracy (P-V): £ 0.15µm / 75mm dia, 250mm convex sphere. Surface Finish (Ra): £ 3.0 nanometers (Test Parts cut in both the X-Z and Y-Z planes) (Important Notice: Both form and finish are measured on the same part, same surface!) |
Working Load Capacity (Radial) | 85 Kg @ 7bar (185 lbs @ 100psi.) / 102 Kg @ 10bar (225 lbs @ 145psi.) @ spindle nose |
Working Load Capacity (Axial) | 197 Kg @ 7bar (435 lbs @ 100psi.) @ spindle nose |
Axial Stiffness | 228 N/μm @ 7bar (1,300,000 lbs/in @ 100psi) / 260 N/μm @ 10bar (1,500,000 lbs/in @ 145psi) |
Radial Stiffness (@ spindle nose) | 98 N/μm @ 7bar (560,000 lbs/in @ 100psi) / 140 N/μm @ 10bar (800,000 lbs/in @ 145psi) |
Motion Accuracy | Axial: ≤ 12.5 nanometers (0.5μ”) Radial: ≤ 12.5 nanometers (0.5μ”) |
Contact us at info@simtrum.com for customized service